About Window & Door Certification
Certification can be said to have began in 1947, at a time when there was little regulation in the building industry. I that year, the AAMA (American Architectural Manufacturers Association)* began to establish performance standards for fenestration products of all types. This quickly became an indispensable resource for architects, specifiers, contractors and manufacturers seeking to standardize and guarantee product performance.
Product testing and certification is now a required process that enables door and window manufacturers to provide the consumer with a way of verifying the quality of their goods and whether it is the best fit for the needs of their building and location. It also provides a way to objectively compare the products of one company to another.
The industry states that windows and doors need to comply with sections of the International Energy Conservation Code (IECC), International Building Code (IBC), the International Residential Code (IRC), and in Florida, with the Florida Building Code (FBC) requirements.
Local jurisdictions send out building officials/inspectors to job sites where they verify that the window or door products have been tested and certified to the standards required by the local building codes. The inspector checks that the product’s labels for their NFRC energy performance or their WDMA Hallmark performance matches the rating that is required. This information is also typically listed on the builder or architects’ drawings.
So how is this all achieved, you ask? There are a number of different types of testing that a manufacturer has to take into consideration when they are designing and constructing their product.
So how is this all achieved, you ask? There are a number of different types of testing that a manufacturer has to take into consideration when they are designing and constructing their product.
01. The first is testing for the Energy Performance rating, which is accomplished through the National Fenestration Rating Council (NFRC). These tests take into consideration the design of your product from the frame and sash, all the way down to the glass and spacers used. This test requires a computer simulation of the products functionality, which is then physically tested and validated through a 3rd party testing laboratory. From there the product results get sent to another 3rd party certification agency for review and approval. After final approval, a certification number is assigned and the products can be labeled with the NFRC ratings they achieved
02. The second group of tests, evaluate the air, water, structural and forced entry performance according to the AAMA/WDMA/CSA 101/I.S.2/A440 (also known as NAFS) or TAS 202 requirements. The actual product is built and sent to a 3rd party testing laboratory to have the above testing performed on the actual specimens that are installed into a wood, steel or concrete rough opening to simulate an actual condition upon installation. Within the NAFS standard are these individual standards per American Society for Testing and Materials (ASTM).
Air Infiltration: The product gets tested for air infiltration and exfiltration per ASTM E283 to determine the leakage rate across the entire specimen.
Water Infiltration: The next test is the water penetration test by uniform static air pressure difference per ASTM E331 or ASTM E547 to make sure products do not let water into the interior of the building. This measures the competence of seals as well as the integrity of the entire product itself.
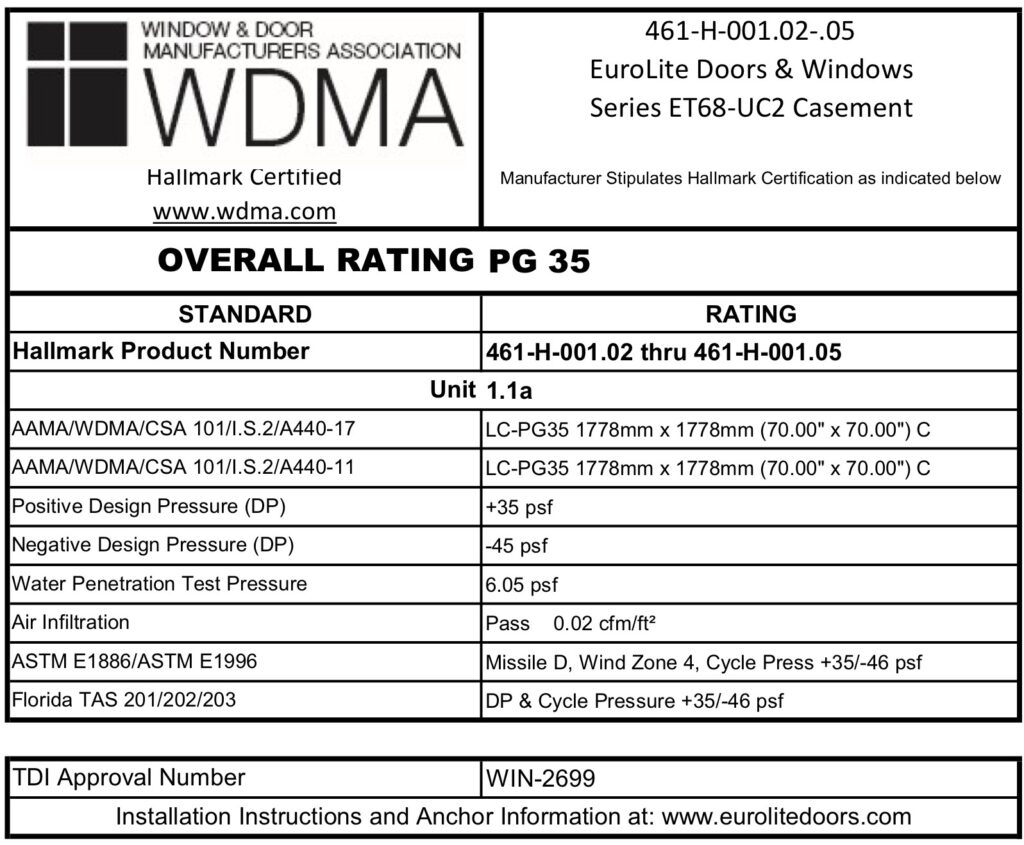
Structural Integrity: Next is the structural test per ASTM E330 to determine the structural performance of the exterior window or door. For example: The Design Pressure required is 50 psf. The window or door is preloaded to ½ the design pressure (25 psf), then loaded to full design pressure (50 psf) while deflection measurements are taken. Then it is loaded to 1-1/2 times design pressure (75 psf) and permanent set of the longest unsupported span is taken. The deflection and permanent set results must fall within the accepted amount per the design pressure being tested. This is done for positive pressure and then for negative pressure.
Forced Entry: The forced entry test on a window differs from that of a door. The window requires testing to ASTM F588 and swing doors require testing to ASTM F467 and sliding doors to ASTM F842. This is to test the integrity of a structure with a given amount of force applied to the product and its components in an attempt to gain entry.
Operational Functionality: All products also require extra auxiliary testing according to the product. For example, a Side Hinged Door requires testing to AAMA 920, which requires the door to be operated open/close for a set amount of time. The total number of applied cycles increases with the Performance Class for which the door is intended, ranging from 25,000 for R Class doors up to 500,000 for AW Class doors.
Once the testing is completed and the unit passes all the required test procedures, a test report is written. From there the product results get sent to a 3rd party certification agency WDMA Hallmark for review and approval. After approval, a certification number is assigned and the products can be labeled with the product class and rating they achieved.
03. High Velocity Hurricane Zones: The third type of testing is for High Velocity Hurricane Zones (HVHZ) which requires impact and cyclic testing for specialty areas like Florida or along the coastal regions where hurricanes typically make landfall. Along with the other testing already mentioned, these areas require testing to the ASTM E1886/E1996 or the TAS 201/203 protocols. These tests are performed to determine the performance of the fenestration product installed into buildings, which are subjected to impact and cyclic static pressure differentials to simulate the windborne debris and pressures during a hurricane. For example: If your product is trying to meet Missile Level D, a 9lb 2×4 is shot out of a cannon at 50 ft/sec (34 mph). Each specimen is impacted either 1 or 2 times in each infill (glazing) to make sure it can withstand windborne debris. If there is no tear or opening through which a 3” in diameter sphere can pass, the unit is then cycled for 4500 times positive pressure, and then 4500 time for negative pressure. The unit is checked 1 final time for any tears or openings.

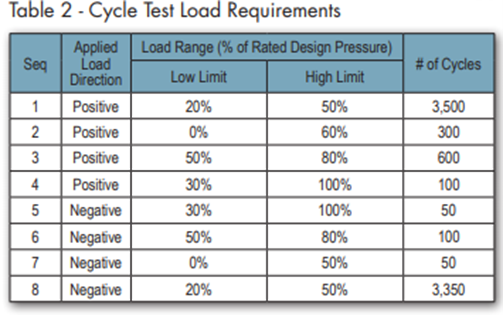
Once the testing is completed and the unit passes all the required test procedures, a test report is written. From there the product results get sent to a 3rd party certification agency WDMA Hallmark fo review and approval. After approval, a certification number is assigned and the products can be labeled with the product class and rating they achieved.
4. Quality Assurance Management System: Besides all the above testing that has to be performed on the products, the manufacturer is also required to maintain a Quality Assurance Management System that meets the requirements of the 3rd party certification agencies. This is required to ensure that the products that were tested and certified are still being produced in the same way as they were built for the test specimens. To establish this, the 3rd party certification agency goes to the manufacturing premises to perform an onsite audit of the Quality System and records, as well as inspecting products per the test reports and drawings. This process is for both the NFRC and WDMA Hallmark certifications.
5. Fire Rating: The fourth type of testing is for fire ratings. We are not currently rated for fire, but steel and glass with extra safety seals are generally fire safe for up to 10 minutes.
All of these tests are performed to protect the public health, safety and general welfare of the occupants of a building. It is also an objective means to evaluate the strength, durability and energy efficiency of the window or door products that you choose.
* On January 1, 2020, AAMA and IGMA (Insulating Glass Manufacturers Alliance) merged into one organization, the Fenestration and Glazing Industry Alliance, or FGIA.